Denim clothing is a kind of fashionable and popular clothing fabric, which is deeply loved by the public. With the improvement of people’s living standards, the demand for garment fabrics is higher and higher. Denim clothing has developed from the original durable and simple work clothes to multi variety and diversified clothes. Classic denim refers to the Coarse Count Twill Fabric Made of pure cotton yarn, warp dyed with indigo dye or sulfur dye and natural color weft, which is interwoven with three upper, lower and right twill weave. The woven grey cloth should also be finished by desizing, singeing, mercerizing, preshrinking or setting. After making clothes, it also needs washing water and surface modification of various processes to create colorful and fashionable denim clothes.
With people’s higher and higher requirements for denim clothing, the requirements for the color fastness to rubbing of denim clothing are also higher and higher. The low color fastness of denim clothing to rubbing is due to the fact that the dye on the fabric is easy to fall off, which affects the color of clothing. Improving the color fastness to rubbing of denim clothing is an important content to improve the quality of denim fabric and clothing. With rich production experience and through a number of experiments, the author found that the color fastness to friction of denim fabric or clothing is related to dyes, pulp dyeing equipment, pulp dyeing process, finishing process and washing process. Taking all cotton denim fabric as the research object, the author carried out experiments from many aspects to study its influence on the color fastness to friction of denim fabric.
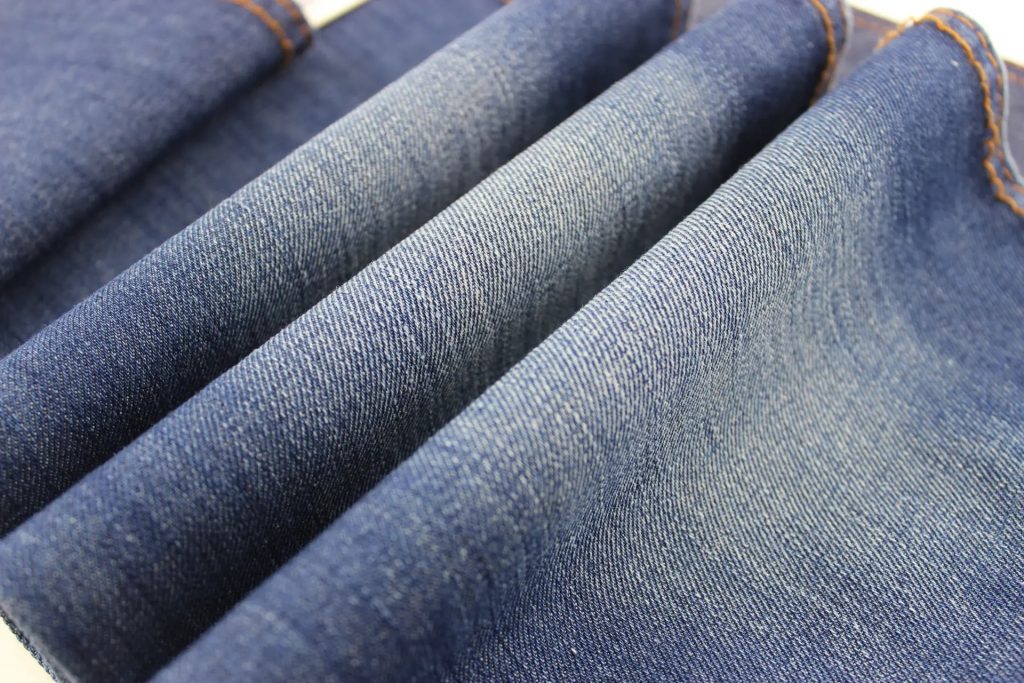
Colour fastness to rubbing
Color fastness to rubbing refers to the fading degree of dyed fabrics after rubbing, which is divided into color fastness to dry rubbing and color fastness to wet rubbing.
In denim fabric, warp yarn is dyed by sizing. Due to the particularity of warp in sizing and dyeing process, the binding force between dye and fiber is low, resulting in low color fastness to friction. Different from the conventional color fastness, the color fastness to rubbing plays a special role in denim fabrics and clothing. Denim has poor color fastness to rubbing, which leads to different washing effects of denim clothing; However, too low color fastness to rubbing will not only affect the quality of jeans, but also affect people’s wearing and use.
Analysis of influencing factors
From the dyeing principle of indigo dye, it can be seen that the main factors affecting the color fastness to rubbing of cotton denim fabric are: (1) the shape and particle size of the dye. The smaller the dye particle is, the higher the uniformity is, which is more conducive to improve the color fastness to friction. (2) Dyeing process. As warp dyeing is instantaneous immersion, oxidation is mainly carried out with the help of oxygen in the air. The times of dyeing and oxidation have a great influence on the adsorption of dyes by fibers. (3) Dyeing equipment. Yarn dyeing includes rope dyeing and sheet dyeing. There are great differences in equipment and technology between them, which has a certain impact on the color fastness to friction. (4) Washing of yarn after dyeing. Washing after yarn dyeing is the main process to remove floating color. The more floating colors, the lower the color fastness to rubbing. (5) Pretreatment process refers to yarn pretreatment process. The less impurities the yarn contains, the greater the ability to absorb dyes and the higher the corresponding color fastness to rubbing. (6) Finishing process refers to the process of finishing denim grey cloth, including singeing, desizing, mercerizing and preshrinking, as well as clothing washing. The finishing process is beneficial to remove floating color and improve the color fastness to rubbing. Different finishing processes will have different results.
Satisfactory color fastness to rubbing can be achieved by selecting appropriate dyes, improving dyeing and weaving processes, and remedial measures such as post-treatment process and washing process. Generally speaking, the smaller the dye particle, the lower the dye concentration, the more fully washed, the better the scouring, the better the core penetration, and the higher the color fastness to rubbing and staining; The smoother the cloth, the cleaner the singeing, the heavier the washing water, and the better the color fastness to friction. Various influencing factors show that the better the combination of dye and fiber, the better the color fastness to friction, and vice versa. This shows that the combination between fiber and dye mainly depends on hydrogen bond and van der Waals force