The method of synthesizing color fixing agent with polyvinylpolyamine and dicyandiamide as main raw materials is similar. The general step is to condense polyhexene polyamine (here, the most common polyvinylpolyamine is diethylenetriamine and triethylenetetramine) with dicyandiamide under the action of catalyst. The reaction steps are shown in Figure 1-1. React at a temperature of about 150C for 3-4 hours, and then reduce the temperature of the system to below 80 ℃, The pH value of the lotion was adjusted to 5 with the appropriate amount of ice CH3COOH. Finally, adding the appropriate deionized water, the formaldehyde free fixing agent with solid content of about 28% was prepared.
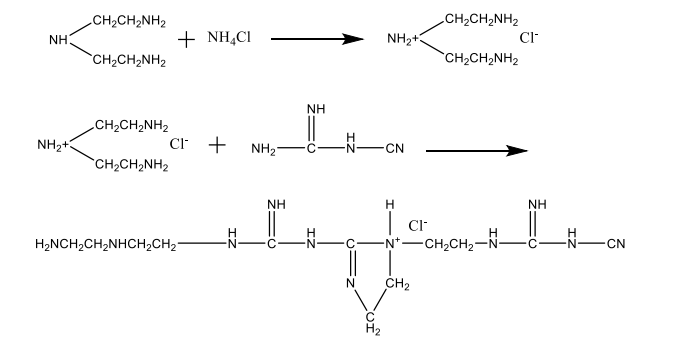
This kind of color fixing agent has an obvious effect on improving the color fastness of dyes, especially direct dyes. For example, Juerg et al. Condensed polyvinylpolyamine and dicyandiamide to form sh-96 color fixing agent. When used for color fixing of reactive dye fabrics, the color fixing fastness is higher because the molecular weight of this color fixing agent is larger than that of general color fixing agents. Therefore, when the fabric passes color fixing treatment, It will be found that there is an obvious force between the color fixing agent molecule and the dye and the fabric, that is, the “molecular gravity” mechanism in the above color fixing mechanism, so as to improve the fixation fastness of the dye. However, the biggest disadvantage of this kind of color fixing agent is that it will cause serious color light changes in the color of the fabric.
Considering the color light change caused by the color fixing agent, Zhou Dongmei and others put polyamine and epichlorohydrin into the reactor as the main reaction raw materials, and prepared an aldehyde free color fixing agent through polymerization. The color fixing agent is called KSS. After the polymerization of the above two raw materials, hydrochloric acid is added to acidify the system to a certain extent to obtain the color fixing agent KS. The purpose of adding hydrochloric acid acidification is to increase the alkali resistance of the dye in the process of color fixing treatment. The color fixing agent can be used for the color fixing treatment steps of cotton fabrics dyed with direct, reactive and sulfide dyes at the same time. In the color fixing process, it is cross-linked with cellulose fibers respectively, reacts with dye molecules, and acts as a “bridge” between fibers and dyes, so as to form a highly three-dimensional cross-linking system, which makes the combination between fibers and dyes more firm through cross-linking, Prevent the dye from falling off easily from the fiber, resulting in color fading, and increase the color fastness of the dye. The molecular chain of the color fixing agent contains a large number of reactive groups. After reacting with the fabric, it will form a three-dimensional network structure on the fiber surface of the fabric. This network film can seal the dye in it, further increasing the color fastness. Moreover, the smooth effect of the film can not only increase the hand comfort of the fabric, but also prevent the dye falling off caused by friction in wet environment. And the biggest advantage of the color fixing agent compared with the general color fixing agent synthesized from polyethylene polyamine is that it has almost no change in color light, which solves the problem of color light.
On this basis, although the color light problem has been solved, with the wide use of this kind of color fixing agent, it is found that this kind of color fixing agent has weak resistance to ultraviolet light, that is, long-term exposure under sunlight, and low sun fastness. Niu Tianyun and others have studied this issue. With triethylenetetramine and epichlorohydrin as the main raw materials, after the preparation steps similar to the above, and through the continuous adjustment of reaction conditions, they finally successfully developed an aldehyde free color fixing agent for reactive dyes, which is used in the color fixing process of fabrics. The treatment method is different from the previous color fixing process, and a small amount of carboxymethyl chitosan will be added in the color fixing process, The effect of this material on improving the sun fastness of the fabric is very significant, because carboxymethyl chitosan has good film-forming performance on the fiber surface, which protects the dye from the influence of sunlight, so as to improve the sun fastness. And other fastness problems have also been greatly improved. The wet rubbing fastness of the fiber treated with this color fixing agent can be as high as grade 4, the staining fastness can be up to grade 5 or above, the dry rubbing fastness can be up to grade 4 or above, the fading fastness can be about grade 3 ~ 4, and the fabric will not have obvious color light change in the morning after color fixing, because carboxymethyl chitosan will react with the negative ions in the dye in the process of color fixing, Wrapping the hydrophilic groups on the dye molecules can not only increase the molecular weight of the dye, but also reduce the water solubility of the dye and increase the overall dyeing effect.
The above two typical color fixing agents are color fixing agents synthesized with polyethylene polyamine and epichlorohydrin as the main raw materials. This kind of color fixing agent is more popular in the market, and the preparation process is simple and easy to use.