With the increasing improvement of people’s living standards, the social requirements for environmental protection in various industries are also gradually improving. As a highly polluting industry, the development of environmental protection and energy conservation in the era of low-carbon economy has become the focus of the industry. Nowadays, with the support of the concept of low-carbon and environmental protection, the dyeing and finishing technology of China’s printing and dyeing industry has developed rapidly, among which the environmental protection and energy-saving dyeing and finishing technology of knitted fabrics is the focus of the development of environmental protection and energy-saving technology in the printing and dyeing industry. Based on the relevant requirements of environmental protection and energy conservation, with the support of advanced science and technology, we should constantly innovate and develop knitted fabric environmental protection and energy-saving dyeing and finishing technology, save resources and energy to the greatest extent, reduce environmental pollution caused by the development of printing and dyeing industry, and promote the green and environmental protection development of printing and dyeing industry.
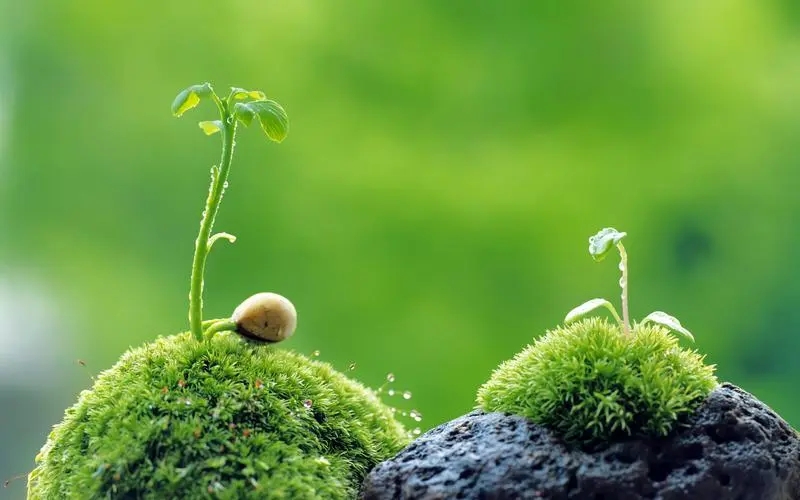
Hydrogen peroxide low temperature bleaching agent technology
At present, hydrogen peroxide bleaching active agents such as sodium nonyloxybenzene sulfonate and 6-acetolactam-p-toluenesulfonic acid have been successively introduced internationally. Hydrogen peroxide low-temperature bleaching technology mainly uses low-temperature hydrogen peroxide bleaching active agent to oxidize and bleach pure cotton knitted fabrics. Compared with the traditional knitting fabric bleaching process, it can reduce the working temperature of pure cotton knitted fabrics to 70 ℃, so as to effectively meet the temperature requirements of knitted fabrics during bleaching, Achieve the effect of environmental protection and energy saving.
Deoxygenase Technology
Biological enzyme technology has the advantages of specificity, high efficiency, low consumption and low pollution, which makes it widely used in textile printing and dyeing industry. With the continuous development of science and technology, more and more new biological enzymes have been developed and utilized, such as cellulose deoxygenase. As a complex enzyme, cellulose deoxidizing polishing enzyme mainly plays the role of delaying the polishing and finishing of pure cotton knitted fabrics or polyester cotton knitted fabrics in the actual application process. The actual purpose is to effectively remove the residual bleaching hydrogen peroxide, wool balls and cellulose on the knitted fabrics after bleaching treatment, so as to make the surface of knitted fabrics bright and clean, and reduce the pilling of knitted fabrics in the actual use process to a certain extent, Bring to knitted fabrics.
Usually, after bleaching, the knitted fabric needs to be removed and polished by deoxygenated polishing enzyme technology, and this process is generally carried out in the same bath as dyeing. After deoxidation polishing, the surface of knitted fabric will become smooth and bright with clear lines. In addition, due to the same bath with dyeing, after the completion of oxidation polishing, the dyeing process of knitted fabrics will also enter the subsequent alkali fixation stage. At this time, there is no need to heat the dyeing solution, and soda ash can be directly added to the dyeing solution for color fixation. The purpose of this process is to inactivate the deoxypolishing enzyme through soda ash to achieve the color fixation effect. Compared with the traditional process, this process can not only save a lot of water resources, but also effectively shorten the whole process by about 1.5h, so as to achieve the effect of environmental protection and energy saving.
Environmental protection and energy saving auxiliary
As a common knitted fabric material in the textile printing and dyeing industry, polyester fiber usually needs to be printed and dyed under high temperature and high pressure of 130 ℃ due to its hydrophobic characteristics. If the temperature demand of polyester fiber dyeing can be reduced, it can not only reduce the temperature, improve the utilization rate of machinery and equipment, reduce energy consumption and shorten the production cycle, It can also avoid the influence of printing and dyeing in high temperature environment on non polyester materials that are not resistant to high temperature in knitted fabrics. The key point of polyester fiber dyeing is to speed up the dyeing temperature of polyester fiber and increase the dyeing efficiency of polyester fiber at low temperature. Compared with the traditional process, the low-temperature dyeing process of polyester fiber can control the dyeing temperature of polyester fiber at 110 ~ 120 ℃, and save the dyeing time of about 0.7h [4], so as to improve the effect of environmental protection and energy saving in many aspects.
Supercritical carbon dioxide dyeing technology
Supercritical carbon dioxide dyeing technology is a dyeing and finishing technology with carbon dioxide as the medium. Because the carbon dioxide in the practical application of the technology can realize the effect of repeated recycling, compared with the traditional dyeing process, it can effectively save all kinds of media materials and achieve the effect of environmental protection and energy saving. Specifically, supercritical carbon dioxide dyeing technology is mainly used for swelling and plasticizing synthetic fibers such as polyester knitwear with strong hydrophobicity. In the process of practical application, when the temperature of supercritical carbon dioxide fluid is heated to the glass transition temperature of synthetic fiber, the macromolecular chain on the surface of synthetic fiber will creep, so as to improve the escape rate of dyeing solution on knitted fabric and shorten the dyeing and finishing time of knitted fabric. Combined with the actual situation, supercritical carbon dioxide dyeing technology is mainly suitable for the dyeing and finishing of polyester and other synthetic fiber knitted fabrics; Compared with the traditional dyeing and finishing process, supercritical carbon dioxide dyeing technology has the advantages of fast dyeing rate, strong uniformity, excellent dye permeability and good reproducibility , which promotes the popularization and application of relevant technologies in the current textile printing and dyeing industry to a certain extent. In addition, after the knitwear is dyed and finished by supercritical carbon dioxide dyeing technology, there is no need to carry out subsequent cleaning, drying and other processes. Moreover, supercritical carbon dioxide dyeing technology is completely dyed and finished by carbon dioxide, which will not produce harmful gases in the process of treatment and will cause relatively less environmental pollution. Therefore, the application of supercritical carbon dioxide dyeing technology can effectively reduce sewage discharge and harmful gases.The pollution to the environment caused by body discharge can reduce the consumption of water resources, so as to achieve the effect of reducing pollution and protecting water resources