Since entering the 21st century, the contradiction of large resource consumption and large pollutant emission in the production process of China’s textile industry has become increasingly prominent, which is directly related to the sustainable development of the textile industry. Therefore, promoting energy conservation and consumption reduction and environmental protection production in the textile industry is an important and urgent task for the whole industry. The energy consumption of printing and dyeing industry accounts for about 60% of the energy consumption of the whole textile industry, which is the focus of energy conservation in the textile industry.
In the process of printing and dyeing, the pretreatment of cotton fabric mainly includes desizing, scouring and bleaching, which belong to wet treatment processing. Not only the process is lengthy and needs to consume a lot of water and energy, but also produces a lot of waste water and waste gas to pollute the environment, which is the most seriously polluted link. The purpose of cotton fabric pretreatment is to remove all kinds of impurities, including pectin, wax, ash, pigment, cottonseed shell on natural cotton fiber, as well as size and dirt after warp sizing, so as to improve the whiteness and water absorption of the fabric to meet the needs of subsequent processing. Therefore, the quality of pretreatment plays a key role in the quality of finished products.
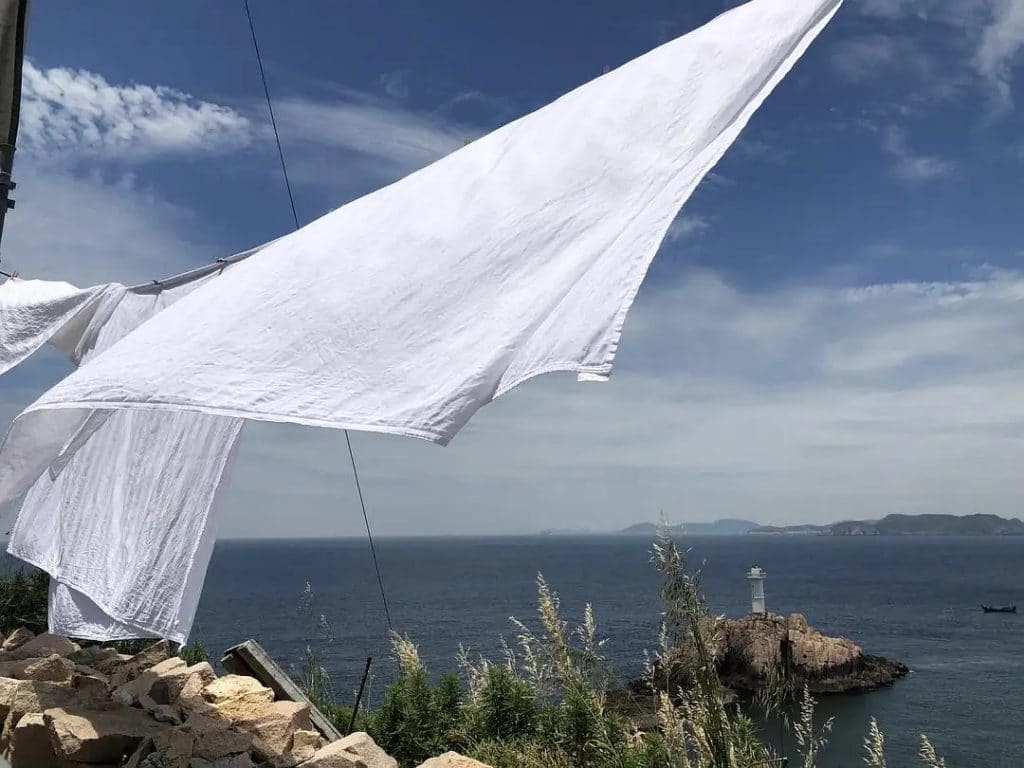
Bleaching is an important process in the pretreatment of cotton fabric. It can remove the natural pigment of cotton fabric and improve the self brightness and brightness of the fabric. Since the middle of the 20th century, hydrogen peroxide bleaching process has been popularized in the dyeing and finishing industry. Due to its good whiteness, good stability, no corrosion to equipment and environmental pollution, it is suitable for the bleaching of a variety of fibers, which makes it quickly applied in the printing and dyeing industry. Especially with the increasing awareness of environmental protection all over the world, the adsorbable organic halide (AOX) has become the wastewater discharge limit index, The application of hydrogen peroxide bleaching process is further strengthened.
Excellent judgment . however, the traditional hydrogen peroxide bleaching process takes a long time, not only has high energy consumption, but also has great damage to fibers, which restricts the further development of hydrogen peroxide bleaching process. While the textile printing and dyeing industry has achieved rapid development, the contradiction between energy saving and consumption reduction and environmental protection has become increasingly prominent. Therefore, the fabric is bleached at low temperature by using the catalyst with high catalytic activity as an energy-saving pretreatment The research and development of technology is of great practical significance.
After scouring, the appearance of cotton fabric becomes clean and soft, and the water absorption of the fabric has been greatly improved, but the natural pigment has not been removed, and the whiteness of the fabric has not been improved greatly, which can not meet the quality requirements of bleaching products. Therefore, the refined cotton fabric should be bleached.
There are many influencing factors in the bleaching process, such as the concentration of bleaching agent, pH value, temperature, time, stabilizer or activator, which will affect the bleaching quality of cotton fabric. In cotton fabric bleaching, the commonly used bleaching agents are oxidizing substances, including sodium hypochlorite, sodium chlorite, hydrogen peroxide, etc. Sodium hypochlorite bleaching process can not be applied to the bleaching of protein fibers such as wool and silk. It will destroy the protein fibers and make the fibers yellow.
At the same time, the bleaching waste liquid contains effective chlorine, It will produce non biodegradable adsorbable organic chloride AOX , it will bring AOX pollution, which does not meet the needs of ecological and environmental protection, which limits the application of this process in production; sodium chlorite has good bleaching whiteness, but it will release toxic and corrosive chlorine dioxide gas in the bleaching process, which has high requirements for machinery and equipment and high bleaching cost, which limits its application PJ; hydrogen peroxide, as an important chlorine free bleach, has high whiteness, good stability, no yellowing and is suitable for bleaching It is used for all kinds of fibers and can adopt a variety of processing processes. The final decomposition products are water and oxygen, which has little environmental pollution and is deeply welcomed by printing and dyeing enterprises.