Pure cotton gauze is made of cotton through weaving, scouring, bleaching and other processes. After pretreatment, gauze can remove natural impurities and oil stains on the fabric. However, the traditional gauze boiling and bleaching process needs to be carried out at a high temperature of 100 ℃, which needs to consume a lot of energy. At the same time, it needs to be carried out under strong alkaline conditions. The process flow is long and complex, and the wastewater pollution is serious. In recent years, more and more attention has been paid to the biological enzyme process, mainly because the enzymatic reaction conditions are mild and can be carried out at low temperature and near neutral conditions. The enzyme itself is non-toxic and will not produce toxic impurities in the reaction process, which meets the requirements of national green dyeing and finishing. At the same time, biological enzyme has high efficiency and specificity. It has unique advantages in cotton fabric treatment, less damage to fiber and good wettability. Therefore, biological enzyme pretreatment is a recognized processing method that meets the requirements of environmental protection.
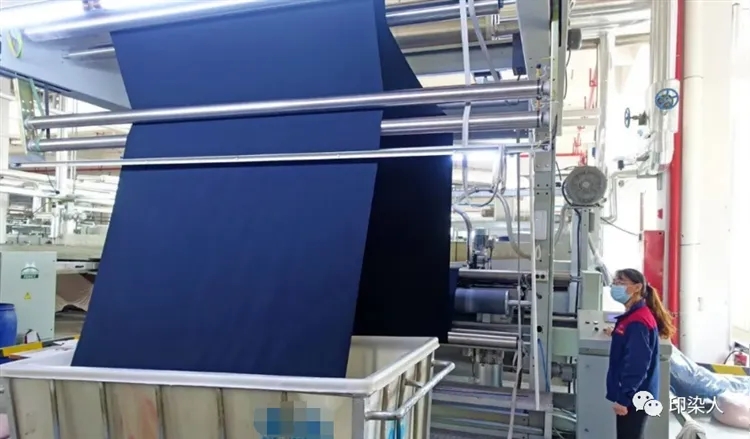
Scouring enzyme JLC and bleaching activator were added to the one bath two-step pretreatment system of cotton gauze, and the scouring enzyme can shorten the settling time of the fabric. With the increase of the mass concentration of scouring enzyme JLC, the sedimentation time of pure cotton gauze gradually decreases. Under the action of scouring enzyme, with the extension of scouring time, the content of pectin, wax and other impurities in gauze decreases, and the sedimentation time of gauze decreases. With the increase of pH value of scouring and bleaching solution, the wettability of pure cotton gauze increases gradually. When the pH value of solution is about 8, the settlement time of fabric is 0.83.
The pure cotton gauze was pretreated with biological enzyme in one bath and two steps. The boiling and bleaching temperature could be reduced by using activator and biological enzyme. Taking the settling time and whiteness of the gauze after scouring and bleaching as the evaluation indexes, the optimized gauze scouring and bleaching process is obtained: the first step is to add scouring enzyme JLC 14 g / L, the scouring time is 40 min, the scouring temperature is 65 ℃, the pH value is 8, and the settling time of the treated gauze is less than 1 s; In the second step, 16 g / L hydrogen peroxide was added, the bleaching temperature was 80 ℃, the bleaching time was 70 min, the whiteness of gauze treated with 6 g / L tetraacetylethylenediamine (TAED) was 78.1, the whiteness of gauze treated with 8 g / L acetylguanidine was 78.2, and the whiteness of gauze treated with 4 g / L oxygen bleaching accelerator was 77.5. It meets the requirements of the factory for gauze pretreatment, and achieves the purpose of energy conservation, emission reduction and green dyeing and finishing. In the scouring and bleaching system, different activators have different effects on the breaking strength of gauze, and the activator tetraacetylethylenediamine (TAED) has the least damage to the strength of gauze.