Synthetic thickeners occupy most of the current market and are widely used in many fields. Compared with natural thickeners, synthetic thickeners have incomparable advantages over natural thickeners. For example, synthetic thickeners are not seasonal and are not affected by climate, region and other factors; Synthetic thickener has strong water holding capacity, and it only takes 5 ~ 10min to prepare uniform color paste, while natural thickener generally takes 2 ~ 3H to prepare uniform color paste due to long hydration time; Preservatives are not required for the storage of synthetic thickeners, while preservatives are generally required for natural thickeners; The synthetic thickener has low solid content, and the dyes with affinity for cellulose can be better fixed on textiles; The synthetic thickener has no problem of hardening and browning when fixing at high temperature.
Synthetic thickener is a kind of long-chain polymer, which is a derivative of the substitute of vinyl compounds. The structural formula is as follows:
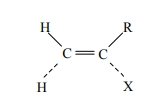
According to different molecular structures, synthetic thickeners can be divided into non-ionic synthetic thickeners and anionic synthetic thickeners. Non ionic synthetic thickeners are mostly lotion derived from polyethylene glycol ether materials. The main products of non-ionic thickeners include lntexa1 hvw of BASF in Germany, acraconz3241 of Bayer in Germany, ryuclye reclueer 400cone of Greater Japan ink in Japan, emu1surm of Matsui pigment in Japan, and fatty acid ester thickener m of Shanghai Auxiliary Factory [18]. The non-ionic thickener is insensitive to electrolytes and has good adaptability and wide application range, but its thickening ability is generally not as good as that of the anionic thickener, and a large amount of kerosene is usually added during use, which limits its development and application [19]; Anionic synthetic thickener is a polymer electrolyte compound with carboxyl and other hydrophilic groups on the molecular chain. Its main products include lutexal hd-70, hit and HSF of BASF, Germany, acraconz C, lambico LM and superlan99 of Bayer, alcoprint PTF of United colloid company, Carbopol 846 and 876 of Goodrich company, ase-75, ase-95 and ase-108 of America. This kind of thickener has good thickening ability, high paste forming rate, good stability during storage and is not easy to breed mold. The color yield of the printed fabric is also high. Its viscosity is less affected by the shear rate, good rheology and is not easy to splash. It also has little impact on the luster of the printed fabric. It is also suitable for the thickening of shiny products. There is no need to add hydrocarbons such as kerosene during use, but it is sensitive to electrolytes and has poor adaptability.
Thickening mechanism of anionic synthetic thickener: due to the ionizable hydrophilic groups such as carboxyl groups on the molecular chain, after alkali neutralization and salt formation, the carboxyl groups on the molecule are easy to ionize. In the ionized state, the negatively charged carboxyl groups repel each other, so that the molecular chain is fully stretched, the viscosity is increased, and a large amount of free moving water is adsorbed. Anionic synthetic thickeners are usually synthesized by polymerization and usually mainly contain three or more monomers. The first monomer (i.e. main monomer) is generally water-soluble, such as acrylic acid, maleic anhydride, methacrylic acid, acrylamide and 2-acrylamide-2-methylpropanesulfonic acid sodium; The second monomer can increase the molecular weight of the synthetic thickener and increase the apparent color yield, generally acrylate or styrene; The third monomer is a monomer with crosslinking effect. Although its dosage is small, it can stretch the molecular chain of synthetic thickener and form a network structure, such as compound n, n ‘- methylene bisacrylamide containing two alkenyl groups, diallyl phthalate, etc.