There are also many kinds of natural polymer thickeners, mainly cellulose, natural rubber, sodium alginate and starchAnd its denatured products. Among them, there are many kinds of cellulose products, among which sodium carboxymethyl cellulose and hydroxyethyl cellulose are the most widely used products.
This kind of thickener is mainly obtained by chemical treatment of natural polymer cellulose. Their thickening mechanism is that the main chain of cellulose molecules associates with surrounding water molecules through hydrogen bonds, the fluid volume of the polymer itself will increase, and the viscosity of the system will also increase, so as to achieve the purpose of thickening. Because its aqueous solution is a pseudoplastic fluid, its viscosity changes with the change of shear rate, and the viscosity of the solution will increase rapidly with the increase of its concentration. It is one of the most widely used thickeners and rheological additives so far.
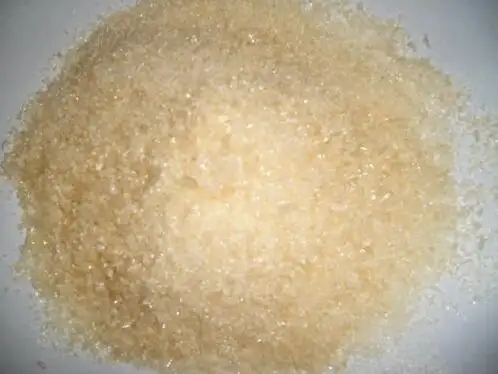
Natural gum as thickener is mainly polysaccharide, mainly including gum Arabic, guar gum, etc; Sodium alginate is the main component of kelp and sargassum. It is mainly composed of sodium salt of alginate. There are three kinds of macromolecular structures, namely polyd-mannuronic acid, polyl-guluronic acid and alternating copolymer. Sodium alginate paste is used for printing with high and uniform color yield, good permeability, clear printed pattern outline, easy washing of printed fabric and soft hand feeling. It is most commonly used in reactive dye printing and is suitable for the printing of cotton, wool, silk, nylon and other textile fabrics.
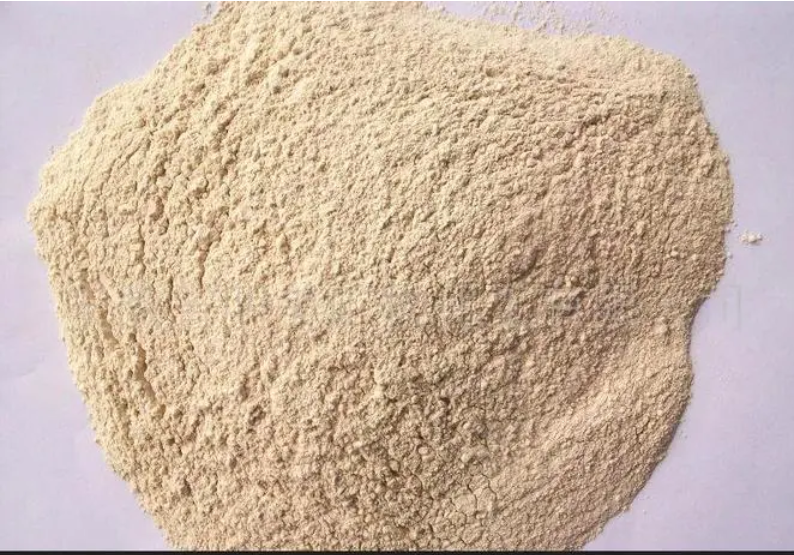
Starch thickener has high paste rate and color yield, and the printed pattern outline is clear. It is applicable to all kinds of dye printing except pigment printing and reactive dye printing. However, due to the large molecular weight of starch, it is difficult to wash away, and the hand feel of the printed fabric is hard, so it is never used alone.