Cotton textile occupies a leading position in the garment industry because of its good moisture absorption, air permeability, easy dyeing, comfortable wearing and good wearing performance. Its market share accounts for 40% of the total fiber consumption in the world. However, when raw cotton fabric is not treated by desizing, scouring, bleaching and other pretreatment processes, the cloth surface turns yellow, feels rough and has poor dyeing performance. Typical cotton fiber contains not only about 90% – 94% cellulose, but also 6% – 10% impurities 2. These impurities are cellulose companion organisms such as pectin, wax, pigment, cottonseed shell and nitrogen-containing substances. Impurities produced in the later processing process such as slurry and oil stains will also affect the wearing performance of cotton fabrics. Unless the cotton fabric is dyed dark or dark, the colored impurities such as natural pigment must be removed by bleaching process before dyeing.
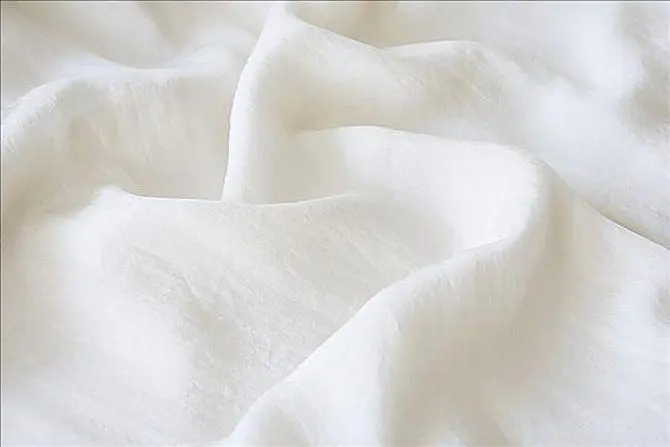
The commonly used oxidizing bleaching agents for cotton fabrics mainly include sodium hypochlorite, sodium chlorite and hydrogen peroxide. Its principle is to destroy the conjugate structure of colored substances on textiles through oxidation reaction to achieve the purpose of bleaching. Among them, there is residual chlorine on textiles after bleaching with sodium hypochlorite and sodium chlorite, which can not meet the environmental protection requirements of no chlorine and no phosphorus. Hydrogen peroxide, as a green and environment-friendly oxidant, is more widely used.
Sodium hypochlorite bleaching: commercial sodium hypochlorite has two forms: solution and powder. Sodium hypochlorite has strong oxidation ability, hydrolysis reaction occurs in water, and the solution is alkaline. The bleaching effect of sodium hypochlorite is complex, and different components may play a role under different conditions. The effective components of bleaching are co, HOCl and Cl2. Generally, the bleaching temperature of sodium hypochlorite is between 20-35 ° C and the bleaching time is 30-60min. The fabric bleached by this method has residual chlorine on the surface, which does not meet the environmental protection requirements of no chlorine and no phosphorus.
Sodium chlorite bleaching: commercial sodium chlorite has two forms: solid and liquid. It is a kind of salt that can be hydrolyzed, and its aqueous solution is alkaline. The composition of sodium chlorite solution is similar to that of sodium hypochlorite. The effective bleaching component is clodan dioxide, which limits its application due to its strong toxicity and corrosivity.
Hydrogen peroxide bleaching: hydrogen peroxide, also known as hydrogen peroxide, is generally a colorless and transparent aqueous solution with concentrations of 27.5%, 30% and 35%, and some as high as 50%. The final decomposition product of hydrogen peroxide is H2O. Because it is green and pollution-free, hydrogen peroxide bleaching is the most commonly used bleaching method in cotton textile industry.