Before the emergence of synthetic dyes, cotton fibers were dyed with plant dyes, mineral dyes and animal dyes until Leeds, England in 1880 Thomas and Robert Holliday of Holliday company developed the application of insoluble azo dyes (ice dyes) on cotton cloth by using the diazo of naphtholamine and sodium naphthol solution. In 1912, ice dye became the most sold cotton dye in the 20th century
Dyeing dyes still have the disadvantages of complex dyeing process, insufficient color yield, difficult color paste storage and high cost, and ice dyeing dyes do not produce real chemical bonding through hydrogen bonding and van der Waals force with fibers, so the color fastness of dyed fabrics can not meet the market demand.
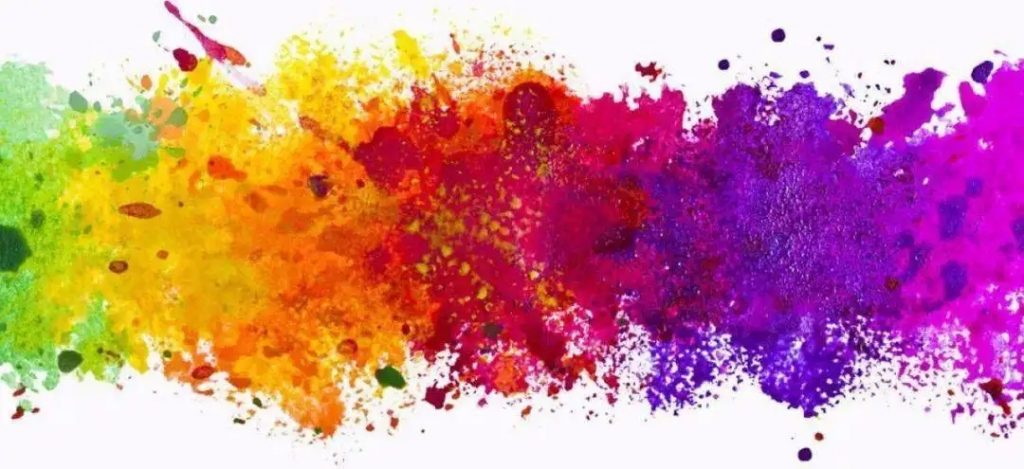
In 1895, cross and Bevan found that covalent bonding was established between cellulose fiber molecules and colored compounds during the treatment of viscose fibers. In 1923, Ciba of Switzerland discovered acid monochlorohydrin dye, which can form wool dye covalent bond with amine groups on wool and obtain good wet fastness. 2] in 1956, ICI company of Britain developed dichlorohomotriazine active dye 3 for cotton fiber on the basis of wool reactive dye cyanuric chloride. Since then, monochlorohydrin type, vinyl sulfonyl, trichloropyrimidine, dichloroquinoline, fluoromonochlorohydrin, monofluorohomotriazine and other reactive dyes have appeared in succession. , Since then, after decades of continuous development, reactive groups with different structures have appeared one after another. Now there are more than 900 kinds of reactive dyes, which has become the most abundant and complete dye in all dyes.
The structural composition of reactive dyes includes: active groups, dye chromogenic matrix, water-soluble groups and connecting groups. In cotton fabric dyeing, reactive dyes form covalent bonds with cellulose fibers. Compared with other cellulose dyes, its advantages are very prominent
(1) Reactive dyes are combined with the dyed fabric through covalent bond, so that the dyed fabric has better washing fastness.
(2) The dyeing process of reactive dyes is simple and easy to realize, and the indexes of dyed fiber materials remain at a high level.
(3) Reactive dyes have bright colors and a wide range of chromatography. Their hue and fastness can meet the requirements of cellulose fiber fabrics in the market.
(4) The price of reactive dyes is low, which is much lower than that of vat dyes for cotton.
However, the low fixation rate of reactive dyes is its main disadvantage. In the dyeing process, some reactive dyes are hydrolyzed due to high temperature and alkaline conditions to produce non reactive hydrolyzed dyes. Hydrolyzed reactive dyes lose reactive groups, but the dye structure has a certain affinity for the fiber. Therefore, hydrolyzed reactive dyes are similar to direct dyes to form floating color on the fiber surface and reduce the color fastness of the fabric. Color fastness is an important index to evaluate the quality of dyed fabrics. In order to solve the problem of color fastness, it is necessary to soap and wash for many times under high temperature conditions, which not only increases energy consumption, but also produces a large amount of wastewater. Half of the energy consumption, one third of the wastewater and a large part of the total water consumption in the dyeing process are related to the post-treatment process. How to save energy and reduce wastewater on the premise of improving color fastness has become the focus of current research.