Reactive dyes are water-soluble reactive dyes, which are mainly used for dyeing cellulose fibers, protein fibers and polyamine fibers. Under suitable conditions, the active groups in reactive dye molecules can react with amino groups in wool and spandex structures and hydroxyl groups in cotton fabrics to form covalent bonds. At this time, dyes and fibers are combined through covalent bonds. Reactive dyes are easily hydrolyzed to produce hydrolytic dyes under the condition of high-temperature alkaline bath, and these hydrolytic dyes and additives in the dyeing bath will adhere to the dyed fabric, thus affecting the fastness of the dyed fabric. Therefore, after printing and dyeing cotton fabric with reactive dyes, soaping treatment must be carried out in order to remove floating color and prevent dyes from contaminating the fabric again.
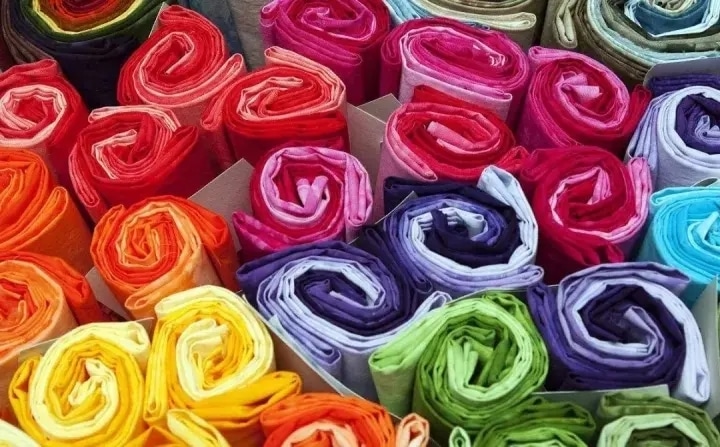
Due to the differences in dyeing process and dye structure, the fixation rate of reactive dyes can not reach 100% when dyeing fabrics. Some dyes are covalently bonded with fibers and are not easy to be eluted by detergents; Some dyes do not bond with fiber, but react with water to form hydrolytic dyes. Although this kind of hydrolytic dyes lose their activity, they have a certain directness to the fiber. They may gather with the dyes that do not react with the fiber and adsorb on the fiber surface to form floating color.
In the process of soaping dyed fabrics, in addition to some dyes and impurities, some auxiliaries and sizes on the fabrics will also be eluted. These washed dyes, auxiliaries and sizes will gradually transfer to the soaping solution. Soaping is carried out at a certain temperature, forming a dyeing bath with dyeing conditions, resulting in the re dyeing of the dyes in light or colorless areas, which is the so-called “white ground contamination”, This will lead to the decline of color fastness of the final product and fabric defects