Polyester / spandex elastic fabric is an important textile fabric. It not only has the properties of fine fabric style, soft touch, long elasticity and good drapability, but also has the advantages of comfortable wearing, free movement, good air and moisture permeability, good wrinkle resistance and wrinkle free crepe. However, the dyeing of polyester / spandex fabrics has been plagued by problems such as poor color fastness, large elastic loss, creases and streaking [12]. In order to solve the above problems, the dyeing process, the selection of disperse dyes and post-treatment were summarized and induction.
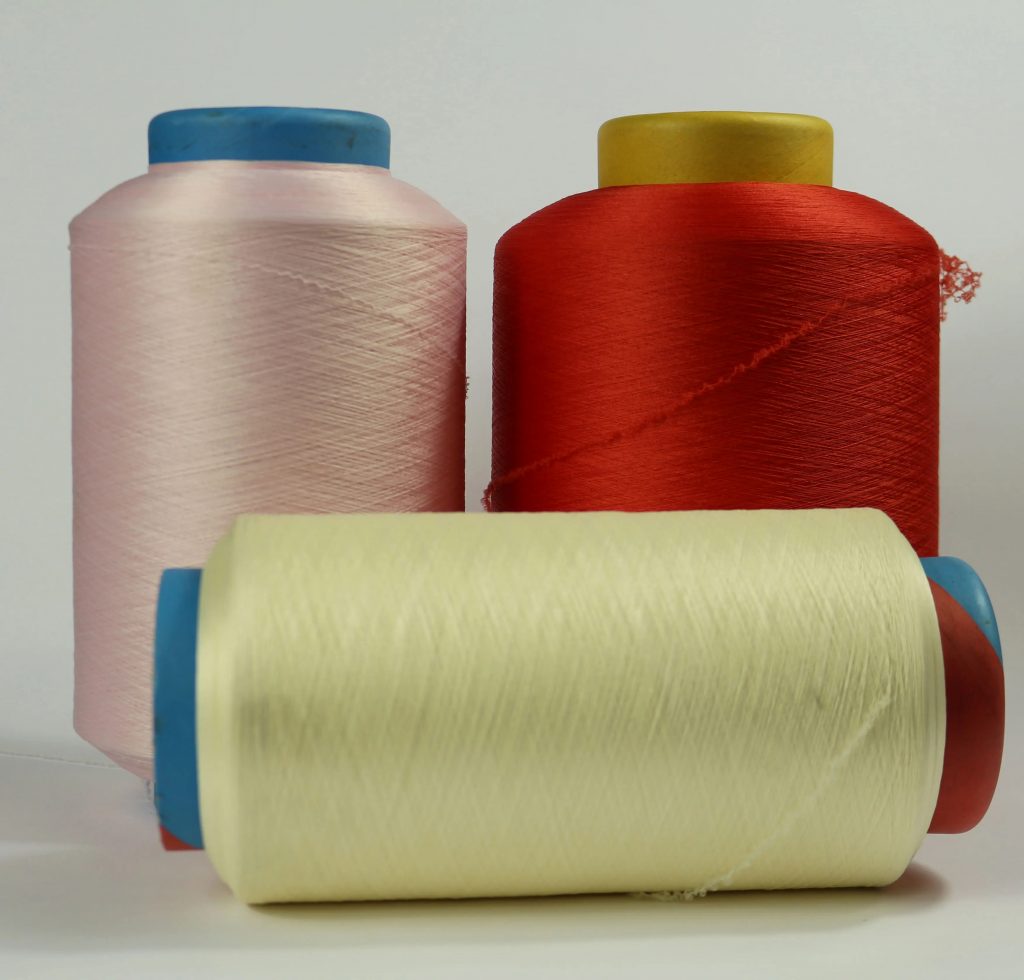
1 disperse dye for polyester / spandex
Disperse dye high-temperature dyeing process is the most commonly used dyeing method at present. From the perspective of disperse dye dyeing mechanism of polyester and spandex, whether low-temperature, medium temperature or high-temperature disperse dyes are selected, due to the existence of spandex fiber more flexible segments with amorphous structure and obvious glass transition temperature difference with polyester fiber. In the process of dyeing and heating up, spandex fiber is easier to obtain dye saturation adsorption, that is, spandex can obtain better dye uptake adsorption rate at 100 ℃, continue to prolong the holding time and increase the dyeing temperature, the adsorption of spandex fiber to disperse dyes is saturated, and the K / s value is almost no longer increased. Due to the high glass transition temperature of polyester fiber, when the dyeing temperature is 100 ℃, the movement of fiber macromolecular segments is limited, the swelling degree of polyester macromolecules is low, and disperse dyes dye less on polyester fiber. The combination of disperse dyes with polyester or spandex fibers is dominated by van der Waals force. Although the polar groups of spandex fibers can bind with disperse dyes by hydrogen bond, it is still difficult to form strong interaction with disperse dyes only by relying on weak interaction van der Waals force and hydrogen bond due to the poor order and high amorphous disordered structure of polyurethane macromolecules,disperse dyes mostly have weak interaction with spandex fiber by floating color, which is the color of spandex fabricThe main reason for poor fastness. It is found that the molecular volume of disperse dyes is moderate, the linearity and coplanarity are good, and they contain an appropriate amount of polar groups, such as – oh and -NH2 has good dye uptake and color fastness to spandex. The dye uptake of disperse dyes to spandex depends on the diffusion rate of disperse dyes in the fiber and the affinity to the fiber. The molecular structure, molecular size and polar groups of disperse dyes will affect the diffusion rate of dyes to the fiber. The key to solve the color fastness of polyester / spandex fabric is to screen the existing disperse dyes and select the disperse dyes with low affinity for spandex or good color fastness to spandex. Among them, monoazo disperse dyes containing ester groups are more suitable for preparing polyester / spandex dyed fabrics with high color fastness. This is because the ester groups are easy to hydrolyze into carboxylates under weak alkaline conditions after alkaline reduction cleaning, which significantly weakens the affinity between disperse dyes and fibers, and makes it easier to remove the disperse dyes adsorbed on the fiber surface. Relatively speaking, The burden of alkaline reduction cleaning is lighter than other disperse dyes. In addition, the liquid disperse dyes developed in recent years, such as MP liquid disperse dyes, can also greatly reduce the reduction and cleaning burden of polyester / spandex dyed fabrics, so as to achieve the obvious purpose of energy saving, consumption reduction and emission reduction.
2.Anti dyeing agent for spandex dyeing
Whether polyester / spandex fabric is dyed by high temperature and high pressure or low temperature carrier, spandex components will give priority to polyester fiber to absorb disperse dyes first, and its dye adsorption capacity is directly related to the content of spandex components. Due to poor dyeing process conditions and dye selection, spandex fiber will lead to supersaturated adsorption of disperse dyes, It directly leads to the increase of post-treatment burden and the decline of color fastness, which is more prominent for high proportion of spandex. In the dyeing process, inhibit or slow down the rapid adsorption of dyes by spandex fiber. For example, adding polyvinylpyrrolidone can preferentially adsorb with spandex fiber and weaken the interaction between dyes and spandex fiber. In this way, it can alleviate the adsorption rate of disperse dyes by spandex fiber and the supersaturated adsorption capacity of dye molecules on the surface of spandex fiber, It can effectively reduce the burden of post-treatment and improve the color fastness of spandex fiber. Wang Zheng [19] used non-ionic surfactant and new high-efficiency reducing cleaning agent SPN to compound, and used the emulsifying and solubilizing effect of additives on disperse dyes to reduce the concentration of disperse dyes in the dyeing bath and weaken the adsorption tendency of disperse dyes to fibers, so as to reduce the concentration of disperse dyes on spandex fibers and reduce the staining effect of disperse dyes on spandex fibers. Wang Yajing et al. [20] studied the anti spandex staining leveling agent fk-4501, with mass concentration of 2G / L, pH value of 4 ~ 7, dyeing temperature of 98 ℃ and dyeing time of 30min; Compared with the conventional leveling agent dyeing process, the color fastness of black polyamide spandex fabric dyed with anti spandex staining leveling agent fk-4501 is improved by more than 0.5, the color depth of cloth surface is increased by more than 12%, and the absorbance of dyeing wastewater is reduced by 90%.
3.Special spandex soaping assistant
The reductive cleaning of polyester / spandex dyed fabric directly affects the color fastness of the fabric, and it is also the main source of high printing and dyeing wastewater. In the reduction cleaning stage, one is to remove the floating color on the fiber surface, especially the disperse dye that is not firmly combined with the fiber on the surface of spandex fiber; The second is to prevent the secondary adsorption (contamination) of the washed disperse dyes on the fiber. Because the reduction cleaning temperature is close to the glass transition temperature of polyester fiber and significantly higher than that of spandex fiber, it is mainly to wash the disperse dyes that are contaminated with spandex fiber. The addition of reducing agent to the reducing cleaning agent will produce achromatic reduction reaction on the chromogenic group of disperse dyes, destroy the structure of disperse dyes, reduce the adsorption of disperse dyes on fibers, and significantly improve the color fastness of dyed products. Due to the diversity of color matching schemes of disperse dyes, there are obvious differences in the influence of reducing agents on dye chromophores. It is difficult to meet the environmental protection requirements of low wastewater discharge only relying on reducing agents. Most reducing agents need to be under alkaline conditions to produce reduction. In addition, under alkaline conditions, they will hydrolyze some disperse dyes that are not resistant to weak alkali. For example, monoazo dyes with ester group in the coupling component and monoazo dyes with cyano group in the diazo component are prone to alkali hydrolysis of ester group and aromatic cyano group under weak alkaline conditions, which can effectively remove the dye floating color on the fiber surface, It can also prevent the hydrolyzed dye from staining the fiber. In the process of reduction cleaning, adding additives 1815, NaBH4 and NaHSO3 can greatly reduce the staining of dyes on polyester and spandex. When isopropyl alcohol and CMC or oil inhibitor CB and AEO-9 phosphate are used at the same time, it can also have a good synergistic effect on the anti staining color of polyester fiber and spandex fiber. Miao Yong et al. [22] used the auxiliary FMES to mix with xl50 and poea15. There is a strong interaction between surfactants, and its combination has good cleaning energy for disperse dyes on spandex; The addition of inorganic salt, organic alcohol and sodium polyacrylate is conducive to the improvement of cleaning ability. Similarly, due to the diversity of commodity schemes of disperse dyes, special spandex soaping additives can not meet the requirements of low wastewater discharge, that is, the weight of post dyeing treatment task depends on the composition of commodity dyes, the proportion of spandex components and the selection of high-efficiency spandex soaping additives. In order to reduce the consumption of water resources, the reduction cleaning of polyester / spandex fabric can not be complete, especially for high proportion spandex fabric, which is easy to cause the decline of household washing color fastness of polyester / spandex fabric in the process of use; In addition, the dyed fabric appears color change in the humid and hot stacking environment, which is a phenomenon of color migration. In serious cases, the existence of residual alkali in the yarn will cause the strength and elasticity damage of spandex.
4.Fabric modification
The dimensional stability of polyester / spandex fabric will affect the quality of dyed products. Due to the high elastic recovery of spandex fiber, the fabric stacking pressure, stacking time and tension will produce creases that are not easy to remove. For example, polyester / spandex fabric will shrink during stacking, and the size of fabric door is unstable. This is because the actual recovery rate of the fabric during stacking is always lower than that of the spandex fiber due to the friction assistance of the outer fiber and the resistance of the weaving point. In the dyeing process, the shrinkage recovery degree of spandex is often different, resulting in irreparable creases, which brings irreparable defects to the subsequent dyeing process. In order to prevent fabric creases in spandex yarn, first, the modified spandex with stable size can be selected. For example, adding specific chain extender to prepare spandex yarn can slow down the creases and other defects in dyeing; The second is to improve the structural stability of polyester / spandex fabric by preheating and setting processing. Due to the poor heat stability of spandex fiber, the heat setting temperature should not be too high and the time should not be too long; Third, it can eliminate the internal stress of the fabric during the previous processing and improve the stability of the fabric through boiling water heat shrinkage. In order to reduce the difference of dyeability between polyester and spandex, polyester / spandex can obtain good dyeability and color fastness by selecting modified polyester or increasing the content of macromolecular terminal primary amine group of spandex; The modified polyester / Spandex Knitted fabric can obtain good dyeability at the dyeing temperature lower than 120 ℃.
Textile products containing spandex fiber are widely used, but there will still be some new technical difficulties in the dyeing and processing of spandex fiber products. How to adopt relatively mild production process conditions can not only improve the color fastness of dyeing, but also reduce the consumption of water resources after dyeing and reduce the color
The occurrence of flower, spandex broken wire, tar spot, chicken claw mark and other problems still need to be comprehensively considered in combination with the properties of spandex fiber. The problems of poor color fastness and elastic damage of spandex containing fabrics can be solved by developing or screening special disperse dyes suitable for spandex dyeing, selecting appropriate dyeing auxiliaries, developing reducing cleaning aids with low water consumption, and taking into account dyeability and low wastewater discharge