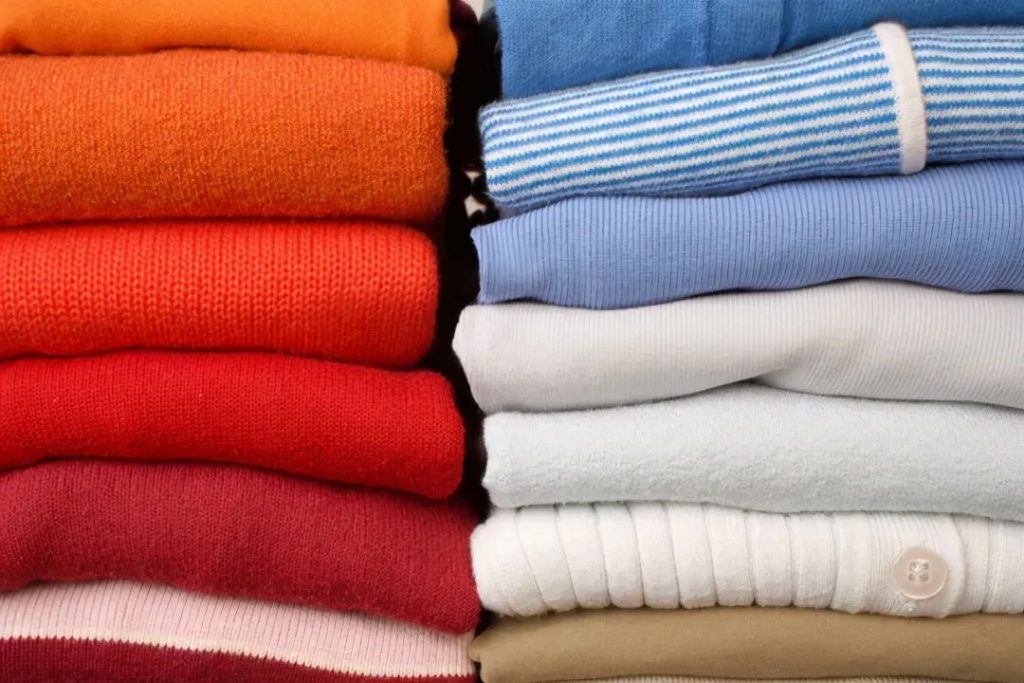
Causes of clothing yellowing
Photoyellowing: photoyellowing refers to the yellowing of the surface of textiles and clothing due to the molecular oxidative cracking reaction caused by the irradiation of sunlight or ultraviolet light. Yellowing is most common in light colored clothing, bleached fabrics and whitened fabrics. After the fabric is illuminated by light, the light energy is transmitted to the fabric dye, resulting in the cracking of the dye conjugate, resulting in light fading and yellow on the fabric surface. Among them, visible light and ultraviolet light are the main factors causing the fading of dyed fabrics with azo dyes and phthalocyanine dyes, respectively.
Phenol yellowing: phenol yellowing is generally caused by the contact transfer of NOx and phenolic compounds. The main reaction substance is usually the antioxidant contained in packaging materials, such as butyl phenol (BHT). Clothing and footwear will be packaged and transported for a long time after leaving the factory. BHT in packaging materials will react with NOx in the air, resulting in yellowing of clothing.
Oxidation yellowing: oxidation yellowing refers to the yellowing of fabrics after oxidation by atmosphere or other substances. Reducing dyes or auxiliaries are usually used in textile and garment dyeing and finishing. After contacting with oxidizing gas, oxidation-reduction occurs and yellowing occurs.
Whitening agent yellowing: whitening agent yellowing mainly occurs on light colored fabrics. When the residual whitening agent on the clothing surface migrates due to long-term storage, resulting in excessive local whitening agent, resulting in clothing yellowing.
Yellowing of softener: when the softener used in the finishing process of clothing is affected by heat, light and other conditions, the cation in it will oxidize, resulting in yellowing of the softened part of the fabric.
Although yellowing is divided into the above five types, in the actual use process, clothing yellowing is usually formed by the superposition of many reasons.
How to prevent clothing yellowing
(1) In the production and processing process, the enterprise shall minimize the use of whitening agent and shall not exceed the yellowing point of whitening agent.
(2) The temperature should not be too high when finishing and setting the fabric. High temperature will oxidize and crack the dyes or additives on the fabric surface, and then cause the fabric to turn yellow.
(3) In the process of packaging, storage and transportation, packaging materials with low BHT content shall be used, and the storage and transportation environment shall be kept at room temperature and ventilated as far as possible to avoid phenol yellowing.
(4) In the case of phenol yellowing of textile and clothing due to packaging, in order to reduce the loss, a certain amount of reducing powder can be sprinkled on the bottom of the packaging, sealed in cartons for packaging for 1 ~ 2 days, then unpacked and placed for 6h, and repackaged after the smell dissipates, so as to repair the yellowing to the greatest extent.
(5) In daily wear, pay attention to maintenance, wash frequently and gently, and do not expose to the sun for a long time.
Test standard for yellowing resistance of clothing
The earliest yellowing test method is mainly the internal test method of textiles by Courtaulds, Marks & Spencer and other companies. After more than ten years of evolution, this method has gradually developed into an international general method, and other different methods have been derived to test the yellowing resistance of clothing fabrics. There are many reasons for clothing yellowing, and the test methods are also different.
Test method for yellowing caused by natural light irradiation: GB / T 8427-2008 test for color fastness of textile products – color fastness to artificial light: Xenon arc. The test principle is to put the sample together with a group of blue wool standard samples in the box, expose it under artificial light source according to the specified conditions, and finally grade the discoloration of the sample with the blue wool standard sample to evaluate the color fastness.
Test method for yellowing caused by ultraviolet light irradiation: GB / T 30669-2014 textile color fastness test – fastness to yellowing and discoloration. The test principle is that after the sample is irradiated under ultraviolet light for a certain time, it is compared with the non irradiated sample, and the discoloration grade is evaluated by gray sample card.
Test method for yellowing caused by phenolic substances: GB / T 29778-2013 “evaluation of potential phenolic yellowing in tests for color fastness of textiles” and Sn / t2468-2010 “test method for phenolic yellowing of import and export textiles”. The test principle is to clamp each sample and control fabric in test paper containing 2,6 Di tert butyl 4-nitrophenol (BHT), Place them between glass plates and stack them together, wrap them tightly with polyethylene film without BH to form a test package, and put them into a constant temperature oven or oven for a certain time under the specified pressure. Evaluate the yellowing order of the sample with the gray sample card, so as to evaluate the possibility of phenol yellowing of the sample.
Test method for fabric yellowing caused by chlorine bleaching: FZ / T 01078-2009 test method for chlorine absorption and yellowing of fabrics. The test principle is to compare the sample with the original sample after chlorine bleaching, cleaning and drying in the washing machine, so as to evaluate the yellowing grade of the sample.
Test method for fabric yellowing caused by air pollutants: GB / T 11039.3-2005 textile color fastness test – color fastness to air pollution – Part 3: atmospheric ozone. The test principle is to place a sample and a control standard sample in the atmosphere with a certain ambient room temperature and relative humidity in the ozone test chamber at the same time, Until the color of the control standard sample fades to the same as the fading standard. The test phase is a cycle, which is repeated until the sample reaches the specified discoloration or reaches the predetermined number of cycles.
Including two test methods of natural light and ultraviolet light: QB / T 4672-2014 test methods of artificial leather and synthetic leather, determination of yellowing resistance, and Hg / t3689-2014 test methods of footwear yellowing resistance.