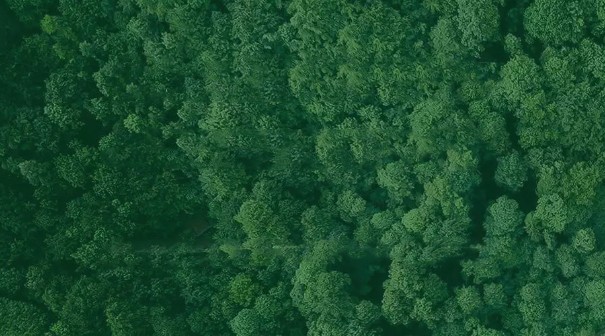
Steam cost is an important cost consumption in printing and dyeing production except for dyes, chemicals, water and electricity.With the continual rising of energy prices and the requirements of environmental protection,how to reduce steam consumption is a problem that printing and dyeing enterprises need to consider ,here are several ways to reduce the consumption of steam.
Process improvement to reduce steam consumption
1. Low temperature pretreatment
Pretreatment includes desizing, degreasing, refining, bleaching and alkali reduction, which are generally carried out at high temperature. After the cold reactor pretreatment, high-temperature water washing is generally carried out to reduce the pretreatment problem, which can intuitively reduce the steam consumption.
In addition to the cold reactor, the realization of low-temperature pretreatment is usually realized through the improvement of additives. For example, low-temperature degreasing requires degreaser with stronger emulsification and dispersion ability at low temperature, and low-temperature bleaching is realized through hydrogen peroxide activator
2. Low temperature dyeing
Low temperature dyeing can generally be realized through the modification of dyes and fibers. Low temperature dyes can reduce the consumption of steam, but usually has lower color fastness than high temperature. How to reduce the dyeing temperature while ensuring the color fastness is the key to the promotion of low temperature dyeing goods.
The modification of fiber can also reduce the dyeing temperature. For example, the modified low-temperature normal temperature and pressure dyeing can reduce the steam consumption.
3. Low temperature post-treatment
Post treatment soaping and reduction cleaning are generally carried out at high temperature. Through the performance improvement of additives, low-temperature soaping and low-temperature reduction cleaning can be achieved, such as oxidation low-temperature soaping agent, surface active compound low-temperature reduction cleaning agent, etc.
Equipment improvement to reduce steam consumption
1. Insulation of equipment
The thermal insulation of printing and dyeing equipment can reduce the heat loss in the process of printing and dyeing production. Good equipment thermal insulation can reduce the loss of steam. This practice has been very mature.
2.Waste heat recovery
Waste heat recovery during printing and dyeing production can also save steam consumption. For example, high-temperature hot water discharged during pretreatment, dyeing and post-treatment can save steam consumption through waste heat recovery. The waste heat recovery of drying and shaping equipment can also achieve the purpose of saving steam.
3. Low bath ratio equipment
Reducing the bath ratio can reduce steam consumption, but the premise is that reducing the bath ratio does not affect the printing and dyeing processing quality, and does not excessively increase the power consumption and washing times.
4. Continuous equipment
Under the condition of sufficient production and processing capacity, appropriate continuous production can also reduce the consumption of steam.
Effective management
1. Reasonable cylinder arrangement and production scheduling of production orders is also one of the important methods to reduce steam consumption. Process improvement and equipment innovation should be well managed, and reasonable and scientific production scheduling will also bring cost savings to enterprises.
2. The statistics and analysis of steam consumption can also help managers make reasonable production plans. For example, the statistics of steam consumption and output of each shift and every day, and the measurement of steam consumption of each process can help managers formulate better production management plans.